Усиление конструкций углеволокном
Если Вам нужно выполнить Усиление конструкций углеволокном — позвоните нам и мы проконсультируем Вас и поможем составить план решения Вашей задачи.
Углеволоконные материалы для усиления конструкций
Усиление конструкций углеволокном – относительно новый для России метод – первые реализованные в нашей стране объекты датированы 1998 годом. Заключается этот метод в наклеивании на поверхность конструкции высокопрочного углеволокна, воспринимающего на себя часть усилий, тем самым повышая несущую способность усиленного элемента. В качестве клея применяются специальные конструкционные адгезивы (связующее) на основе эпоксидных смол, либо минерального вяжущего. Благодаря высоким физико-механическим характеристикам углеволокна, повысить несущую способность конструкции можно практически без потери полезного объема помещений и увеличения собственного веса здания – толщина усиливающих элементов обычно составляет от 1 до 5 мм.
Следует понимать, что «углеволокно» — это материал (например, как бетон), а не конечное изделие. Из углеволокна изготавливают целый набор материалов, некоторые из которых применяются в строительстве – углеродные ленты, ламели и сетки.
В подавляющем большинстве случаев усиление углеволокном применяется для железобетонных конструкций – это обусловлено высокими технико-экономическими показателями реализации таких проектов. Однако, данная технология применима и к металлическим, деревянным и каменным зданиям и сооружениям.
Конструктивные решения усиления углеволокном
При проектировании усиления конструкций углеволокном необходимо руководствоваться Сводом правил СП 164.1325800.2014 «Усиление железобетонных конструкций композитными материалами. Правила проектирования.»
Усиление плит перекрытий и балок выполняется путем наклейки углеволокна в наиболее напряженных зонах – обычно в центре пролета по нижней грани конструкции. Это повышает их несущую способность по изгибающим моментам. Для решения таких задач подходят все виды углеродных материалов – ленты, ламели и сетки.
Кроме того, для балок часто требуется выполнить усиление приопорных зон на повышение несущей способности при действии поперечных сил (по наклонной трещине). Для этого выполняется наклейка U-образных хомутов из углеродных лент, или сеток.
Углеродные ленты и ламели иногда применяются в совокупности, так как их способ монтажа и адгезивные составы схожи. Применение углеродных сеток, как правило, исключает использование лент и ламелей в связи с производством «мокрых» видов работ.
Усиление колонн происходит путем их оклейки углеродными лентами, или сетками в поперечном направлении. Таким образом достигается эффект «бондажирования» и происходит сдерживание поперечных деформаций бетона по схожему принципу с «бетоном в трубе», или «трехосным сжатием».
Подготовка поверхности перед усилением углеволокном
При усилении железобетонных конструкций углеволокном выполнение работ начинается с разметки конструкции – отчерчиваются зоны в которых будут располагаться элементы усиления. Затем эти зоны очищаются от отделочных материалов, загрязнений и цементного молочка до обнажения крупного заполнителя бетона. Для этого применяют, либо угол-шлифовальные машинки с алмазными чашками, либо водо-пескоструйные установки.
Качество подготовленного основания (поверхности на которую приклеивают углеволокно) напрямую влияет на совместность работы конструкции с элементом усиления, поэтому при подготовке основания, в обязательном порядке, контролируют следующие параметры:
-
ровность поверхности; -
прочность и целостность материала усиливаемой конструкции; -
температуру поверхности конструкции; -
отсутствие загрязнений и пыли; -
влажность; -
и другие (полный перечень и допустимые значения контролируемых параметров приводятся в технологических картах на выполнение строительных работ).
Приготовление компонентов для усиления углеволокном
Углеродные материалы поставляются смотанными и упакованными в полиэтилен. Очень важно не испачкать их в пыли, которой после шлифования бетона будет очень много, иначе углеродное волокно невозможно будет пропитать связующим, т.е. получится производственный брак. Поэтому, заготовительную зону следует застелить плотным полиэтиленом и уже по нему отматывать требуемую длину углеродного материала. Обрезка углеродных лент и сеток может осуществляться канцелярским ножом, или ножницами по металлу, а углеродных ламелей – угол-шлифовальной машинкой с отрезным кругом по металлу.
Адгезивы, как правило, применяются двухкомпонентные – т.е. требуется смешивать два материала в определенной пропорции. Необходимо четко следовать инструкции производителя и при дозировании использовать весы, или мерную посуду. Смешивание составов происходит путем постепенного добавления одного компонента в другой при постоянном перемешивании низко оборотистой дрелью. Ошибки дозирования, или неправильное вмешивание одного компонента в другой, могут привести к закипанию адгезива.
В последние годы, большинство производителей поставляют адгезив в комплектах – т.е. в двух ведрах с уже дозированными объемами компонентов. Таким образом можно просто вмешать содержимое одного ведра в другое (ведро специально поставляется большего объема (полупустым)) и получить готовый адгезивный состав.
Полимерцементные адгезивы (для углеродных сеток) поставляются в мешках и затворяются водой согласно инструкции, как любой ремонтный материал.
Следует помнить, что адгезив имеет ограниченный срок жизни – порядка 30-40 минут и он резко сокращается при повышении температуры выше 20°С, поэтому объем приготовляемого адгезива не должен превышать физических возможностей его выработки.
Монтаж углеволоконных материалов
В зависимости от вида углеволоконного материала технология его монтажа существенно отличается:
Монтаж углеродных лент может осуществляться по «мокрому», или «сухому» методу. В обоих случаях на основание наносится слой адгезива, но при «мокром» методе углеродная лента сначала пропитывается адгезивом, а потом прикатывается валиком к основанию, а при «сухом» — лента прикатывается к основанию, а потом сверху ее пропитывают слоем адгезива. Пропитка углеродной ленты осуществляется путем нанесения на ее поверхность слоя адгезива и вдавливания его малярным валиком, или шпателем, добиваясь того, что бы верхний слой связующего проник вглубь углеволокна, а нижний слой связующего вышел наружу. Углеродные ленты могут укладываться в несколько слоев, но при наклейке на потолочную поверхность, не рекомендуется за одну смену выполнять более 2-х слоев – материал начинает «сползать» под собственным весом.
Следует помнить, что после полимеризации адгезива, его поверхность будет гладкой и качественно нанести на нее отделку будет невозможно. Поэтому, еще по «свежему» элементу усиления необходимо нанести слой крупного песка.
При монтаже углеродных ламелей адгезив наносится и на конструкцию, и на усиливающий элемент. После этого, ламель прикатывается к основанию малярным валиком, или шпателем.
Монтаж углеродной сетки выполняется на увлажненную поверхность бетона. Сначала наносится первый слой полимерцементного состава. Он может наноситься как ручным, так и механизированным способом – торкретом. По «свежему» слою полимерцемента раскатывается углеродная сетка с небольшим вдавливанием в состав. Удобнее всего это делать шпателем. Затем необходимо выдержать технологическую паузу до начала схватывания состава. Срок схватывания зависит от выбранного состава и температуры окружающей среды, но требуемое состояние – полимерцемент с трудом продавливается пальцем. После этого наносится закрывающий слой полимерцемента.
Защитные покрытия углеволоконного усиления
Необходимо помнить, что адгезивы на основе эпоксидных смол горючи, а кроме того подвержены охрупчиванию при воздействии ультрафиолетовых лучей. Поэтому, применяя их необходимо предусматривать огнезащиту углеволоконных элементов усиления до класса огнестойкости не ниже заявленного для усиливаемой конструкции.
ООО «ПСК Сигма-Ф» выполняет полный комплекс работ по усилению конструкций углеволокном — бесплатный выезд на объект для сбора объемов работ, разрабатывает проект (наличие СРО), осуществляет поставку материалов, выполняет строительные работы, проводит натурные испытания и несет гарантийные обязательства — позвоните нам, и мы рассчитаем стоимость работ на Вашем объекте.
Другие материалы по теме «Усиление углеволокном»:
стен, колонн, железобетонных плит, перекрытий, балок и отверстий в Москве
Технология проведения работ
Усиление углеволокном стен, фундамента, проёмов, плит проводится подрядчиком в несколько этапов:
1. Подготовка обрабатываемой поверхности. С армируемого участка удаляют выкрошенные частицы, счищают пыль, грязь. Избавляются от следов лакокрасочного слоя, шпатлёвки, штукатурки. Выступающие стальные элементы зачищают от ржавчины, при необходимости — заделывают в бетон.
2. Устранение геометрических дефектов. Чтобы композитная панель легла ровно, глубокие трещины, впадины зачеканивают, возвышающиеся выступы — нивелируют с защищаемой поверхностью.
3. Полное удаление пыли. После второго этапа остаются частички загрязнений. Перед началом основной работы колонны, стены, перекрытия снова очищают.
4. Раскрой холста, ламели из углеродного волокна. Мастер вырезывает согласно проектной документации укрепляющие фрагменты, подготавливает их к установке.
5. Разметка области нанесения подготовленных армирующих элементов. Без этого шага могут образовываться некрасиво выглядящие, снижающие прочность «пересечения» холстов — или отдельные участки останутся незащищёнными.
6. Нанесение на одну или обе стороны углеволокна адгезионного (клеящего) слоя. Для создания прочной связи «Вармастрой» применяют эпоксидную смолу с присадками. Вещество малотоксично, быстро сохнет, отлично схватывается со всеми поверхностями, заполняет поры, мелкие трещины. Для равномерного распределения слоя используют строительный валик.
7. Наклеивание полимерного холста, разглаживание посредством шпателя или валика. Последнее позволяет выгнать из-под фрагмента скопившиеся воздушные пузырьки. Сразу после нанесения вырезанный участок можно свободно перемещать на эпоксидном слое, стыкуя с соседними кусками.
8. Нанесение запечатывающего слоя. Внешнее покрытие предотвращает повреждение композитной панели, ускоряет процесс окончательного сцепления клеящего материала, восстанавливаемой и армирующей поверхностей.
Монтаж системы холстов
После высыхания эпоксидной смолы холст или ламель затвердевают, приобретают требуемую жёсткость. Все применяемые материалы сохраняют гибкость: не трескаются, не раскрашиваются, не ломаются при наложении изгибающих усилий.
Усиление конструкций углеволокном, материалы для усиления железобетонных конструкций композитными материалами, технология
Современные промышленная и строительная сферы постоянно развиваются и совершенствуются. Поэтому для решения постоянно возникающих новых задач используются новые возможности. Одна из современных инноваций в этих сферах — использование для усиления конструкций и композитных материалов углеволоконного нетканого полотна.
Особые свойства материала
Чтобы усиление конструкций углеволокном имело смысл, материал обязательно должен отвечать определенными требованиям:
- все волокна должны быть строго параллельными;
- для сохранения структуры необходимо использовать стеклянную сетку или эпоксидный биндер.
Добиться этого удается только при условии изготовления углеволокна в соответствии со строгой технологией. Высокое качество материала возможно, но только при соблюдении технологии производителем.
Если технологический процесс соблюден, углеволокно приобретает уникальные свойства. При своей легкости и минимальной толщине материал очень прочен. Усиление углеродным волокном позволяет существенно улучшить характеристики несущих конструкций уже готовых зданий. А если необходимо добиться повышения прочности несущих конструкций нового строящегося здания, то помогает обеспечить усиление углепластик.
Задания на расчет усиления конструкций углеволокном просим направлять по адресу электронной почты [email protected] или используя форму обратной связи в разделе Контакты.
Консультации о применении материалов осуществляются по телефону: +7 (495) 787-88-28.
Преимущества использования материалов
Ремонтные работы старых зданий, а также строительство новых при условии использования углеволоконных материалов, углепластика или фибробетонов возможно существенное сокращение расходов на работы, сокращение срока их выполнения.
К преимуществам использования этих материалов относится:
- отсутствие необходимости привлекать тяжеловесную технику для работ, так как материалы легкие;
- с применением технологии внешнего армирования время, за которое выполняется усиление бетона углеволокном, сокращается до 10 раз;
- конструкция приобретает способность выдерживать нагрузки, которые в 4 раза превышают допустимый уровень для других материалов;
- конструкция не становится тяжелее;
- материал не подвергается коррозийным изменениям;
- если при проектировании, а также предварительных строительных работах, были допущены ошибки, их вполне можно исправить;
- новые материалы прослужат не менее 75 лет.
Усиление углеволокном проводится быстро и является очень эффективной технологией. При повреждении несущих конструкций усиление углепластиком или углеволокном незаменимо, так как оно помогает существенно уменьшит последствия повреждений, не только вернуть несущие способности конструкции, но и повысить их. В дальнейшем железобетон будет защищен от влияния влаги и возникновения коррозии арматуры. А также от большинства возможных механических повреждений.
Усиление несущих конструкций рационализирует строительство. Но доверить любые работы в этой сфере можно только профессионалам. Ведь огромное значение в достижении необходимого результата имеет технология.
Наша компания гарантирует высокое качество материалов. Усиление железобетонных конструкций композитными материалами нашего производства отвечает заявленным характеристикам. Большое количество успешно законченных проектов — неоспоримое подтверждение этого.
В ходе производства используется исключительно качественное сырье. Техническая база производства — это исключительно современное исправное оборудование, которое не дает сбоев, чтобы усиление железобетонных конструкций композиционными материалами могло принести желаемый результат.
Усиление композитами становится все более распространенной и часто применяемой технологией, поэтому и технология производства отдельных композиционных материалов и систем внешнего армирования — это та ниша, попасть в которую стремится все больше предприятий. Но только при условии технически грамотного подхода и отказа от чрезмерной экономии на материально-технической базе возможно создание конкурентоспособного материала.
За соблюдением требований к технологическому процессу при изготовлении материалов для усиления композитом на производстве мы следим очень строго. Контроль качества — это гарантия того, что усиление железобетонных конструкций с применением наших композитных материалов принесет необходимое улучшение несущих способностей и продлит срок службы железобетона.
Не стоит забывать и о том, что снижение затрат ресурсов при выполнении усиления конструкций углепластиком или углеволокном приводит к существенной экономии. Причем качество работ не страдает, а оказывается только лучше, чем при использовании устаревших технологий усиления.
Обращайтесь для дополнительных консультаций, если по теме усиления углепластиком по технологии внешнего армирования у вас еще остались вопросы. Сделайте современный выбор в пользу усиления конструкций композитными материалами!
Как сделать усиление бетона углеволокном (бетонных и железобетонных конструкций)
Усиление бетона углеволокном – сравнительно новый для отечественной ремонтно-строительной сферы метод, который в России впервые был реализован в 1998 году. Суть метода заключается в наклеивании на поверхность нуждающейся в укреплении конструкции высокопрочного углеволокна, которое забирает часть усилий на себя и существенно повышает несущую способность упрочненного элемента/конструкции.
В качестве клеящего вещества обычно применяют специальные конструкционные связующие с высокой адгезионной способностью, сделанные на базе эпоксидных смол или минеральных составов.
Благодаря тому, что углеволокно обладает высокими физико-механическими свойствами, несущая способность конструкции повышается без потери полезного объема коробки и увеличения собственной массы здания. Обычно толщина усиливающих элементов варьируется в диапазоне 1-5 миллиметров.
Чаще всего реализуют усиление железобетонных конструкций, что объясняется высокими технико-экономическими показателями выполнения работ подобного типа. Но сама технология может применяться к зданиям/сооружениям из металла, дерева, камня и других материалов.
Применение углеродного волокна наиболее оправданно, так как материал считается самым недорогим и эффективным для исправления ошибок в проектировании, выполнении разного типа строительных работ.
Каким требованиям должно отвечать углеволокно:
Параллельное расположение волокна в структуре материала.
Для сохранения структуры армирующих элементов применяется специальная стеклянная сетка.
Углеволокно должно производиться в точном соответствии с технологией, соответствовать высоким стандартам качества.
Изготовленный по правилам материал демонстрирует уникальные свойства – обладает небольшим весом, не дает дополнительной нагрузки по весу, при минимальной толщине дает максимальную прочность. Армирующие углеволоконные элементы используются для усиления уже созданных конструкций и тех, что находятся еще в процессе строительства.
Преимущества композитных материалов
Содержание статьи:
Усиление конструкций углеволокном представляет собой современный эффективный метод, демонстрирующий целый ряд явных преимуществ. Технология внешнего армирования ЖБ конструкций композитными материалами дает возможность выполнить процесс быстро и увеличить несущую способность конструкции в среднем в 4 раза (если сравнивать с иными материалами).
Основные достоинства усиления углеволокном:
Отсутствие необходимости привлекать для выполнения работ специальную технику благодаря малому весу материала.
Длительный срок эксплуатации (до 75 лет) – углеволокно не боится коррозии, агрессивного воздействия внешних факторов.
Нагрузка на здание не увеличивается, так как вес волокна минимален.
Возможность исключить серьезные эксплуатационные проблемы, появляющиеся в случае повреждения конструкций, минимизировать последствия повреждений.
Защита бетона от влаги, арматуры внутри монолита от коррозии благодаря способности волокна создавать водонепроницаемый плотный слой.
Высокая прочность на растяжение – материал демонстрирует значения в диапазоне 4900 МПа.
Простота, высокая скорость монтажа, что позволяет усилить любую конструкцию в малые сроки и без существенных затрат на привлечение людей, техники.
Работы можно проводить без остановки производства, движения транспорта.
Существенная экономия на трудозатратах, времени, финансах.
Общий принцип технологии простой – углеволокно наносят на участки бетонной или железобетонной конструкции в местах наибольшего напряжения. Решение конкретных задач может выполняться с применением сеток, ламелей, лент.
Работы проводятся эффективно и быстро. Любой бетонный или железобетонный элемент восстанавливает свои несущие характеристики, становится защищенным от влаги и коррозии, механических воздействий.
Работы по усилению железобетонных конструкций
Усиление конструкций является очень важной задачей любого ремонтно-строительного процесса, связанного с повышением показателей общей прочности здания. Благодаря усилению удается продлить время эксплуатации элементов и конструкций, возвратить им утраченную несущую способность, улучшить свойства. Часто усиление углеволокном актуально при реставрации железобетонных изделий из-за износа, механических повреждений.
Углеродное волокно – это линейно-упругий полимерный композитный материал, который производится из углеродных нитей толщиной 5-15 микрон. Тонкие волокна выровнены и объединены в микроскопические кристаллы, способные успешно противостоять растяжению. Углеродное волокно по техническим свойствам превосходит металл в несколько раз, поэтому используется в аэрокосмической сфере, оборонной промышленности, строительстве.
Одно из основных преимуществ усиления конструкций углеволокном считается простота реализации задачи. Материал просто нужно правильно наклеить на поверхность упрочняемых элементов на специальные адгезионные составы. Ленты из волокна можно крепить на сжатые/растянутые элементы, пролетные зоны изгибаемых конструкций, короткие стойки, консольные системы, гибкие колонны.
После того, как на конструкцию наклеено волокно, на поверхность наносят специальный полимерцементный состав, делают финишную отделку и красят акриловыми покрытиями.
Усиление углеволокном может применяться для бетонных, железобетонных, металлических, каменных, деревянных конструкций. Метод хорошо подходит для стеновых/потолочных проемов, строительных ферм, стен построек/зданий, плит перекрытия, колонн, иных элементов.
Усиление железобетонных конструкций
Любая конструкция со временем может приходить в негодность либо же изначально быть спроектированной с ошибками. Поэтому появляется необходимость в упрочнении.
Когда нужно выполнять усиление строительных конструкций:
Естественный процесс физического старения и износа материалов, элементов.
Перепланировка помещений с внесением изменений в разного типа несущие конструктивные узлы.
Повреждение конструкции с понижением уровня несущей способности.
Потребность в увеличении этажности здания.
Ошибки в первичном проекте.
Усиление для исключения последствий аварийных ситуаций.
Подвижки грунта.
Железобетонные конструкции могут укрепляться такими способами:
- Традиционные методы – устройство обойм и рубашек, наращивание сечения блок, монтаж металлических порталов, установка разгружающих стоек и дополнительной арматуры.
Инновационные – включают укрепление несущих узлов композитными материалами (не только углеволокно, но и кевлар, карбоновое волокно), инъектирование специальными составами (на базе полиуретана, эпоксидной смолы, полимерцементных материалов), технология преднапряжения канатной арматуры (после бетонирования, набора прочности монолитом натягивается напрягаемая арматура и воспринимает нагрузки).
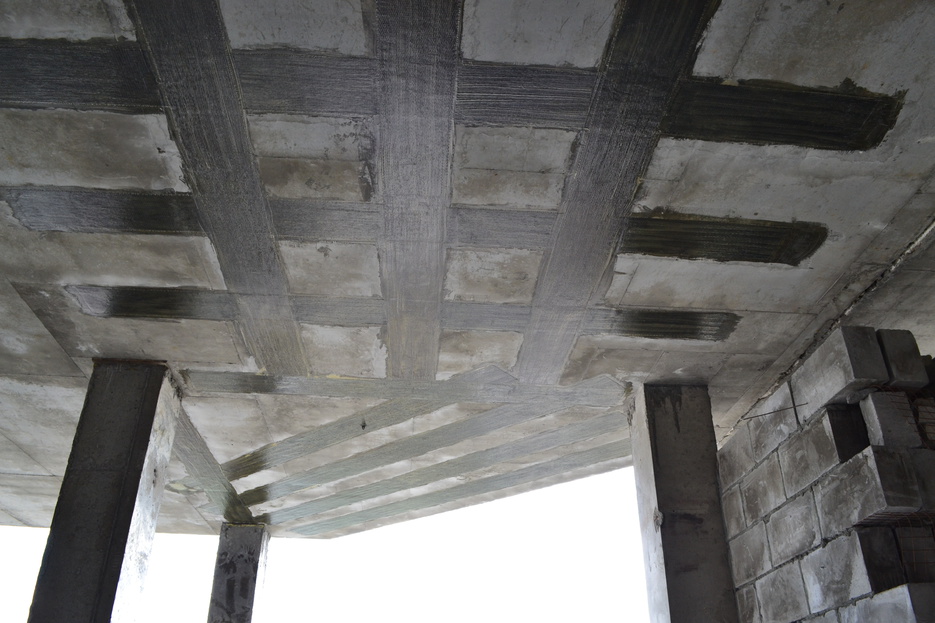
Комбинированные методы – включают одновременно несколько разных способов по индивидуально созданному проекту.
В процессе упрочнения важно отыскать зоны наибольших нагрузок, разметить конструкцию, правильно выполнить подготовительные работы. Участки, на которые планируется клеить композит, нужно тщательно очистить шлифовальным оборудованием. Выбор подходящих методов и решений по упрочнению конструкций осуществляется по проектной документации, созданной на базе исходных данных.
Что учитывается при составлении проекта на усиление ЖБ конструкций:
Результаты обследования, экспертизы объекта (ищут зоны с дефектами и потерей прочности).
Документы по проекту уже созданной конструкции.
Срок эксплуатации объекта.
Информация про гидротехнические и инженерные характеристики участка, которая учитывалась при первичном проектировании, прогнозы возможных подтоплений.
Данные про отличия проектных и реальных значений исполнения узлов, указание отступлений от проекта.
Технологические нагрузки при эксплуатации.
Информация про положение железобетонных конструкций, которая была получена в процессе геодезической съемки.
Реальные характеристики бетона, стали конструктивных узлов.
Все данные про аварийные режимы конструкций, имеющиеся деформации и их причины, про усиленные ранее элементы и узлы.
Сведения про возможные новые нагрузки, ожидания агрессивности среды, особенности эксплуатационного режима.
Как осуществляется усиление конструкций углеволокном:
- Ленты и ламели – с применением адгезивов, с монтажом по общим принципам, поэтому часто данные методы комбинируют.
Углеродная сетка – ее применяют отдельно, так как монтируется с выполнением работ «мокрого» типа.
Поверхность бетона должна быть хорошо подготовлена к композитному усилению – все детали шлифуют по технологии, исключают возможность попадания влаги, удаляют после грязь и пыль. Углеродную ленту можно монтировать сухим/мокрым способом – разница заключается в технологии: в случае применения сухого метода ленту прикладывают к поверхности основания, пропитывают адгезивом.
Если используется мокрый метод – сначала пропитывают, потом монтируют. В таком случае состав наносят на всю поверхность армирующего компонента, дожидаются полного проникновения вещества в структуру и выхода его наружу с бока бетонного основания.
Ламели монтируют так же, но адгезивный состав в таком случае наносят как на бетонную поверхность, так и на армирующий элемент. Сетка углеродная армируется на влажную поверхность бетона.
Усиление перекрытий
Усиление перекрытий углеволокном осуществляется очень часто ввиду того, что материал демонстрирует высокую коррозийную стойкость, не дает дополнительной нагрузки, не меняет внутреннюю геометрию зданий (так как толщина пластины составляет всего 1 миллиметр), долго служит, дает максимальную прочность, не требует применения дополнительного оборудования в процессе выполнения работ. Консервировать объект не нужно, все работы может реализовать небольшая группа работников.
Как выполняется упрочнение перекрытий:
Перекрытия обследуются с целью поиска мест, которые требуют усиления и выполнения расчетов нагрузок.
Создается проект упрочнения перекрытия.
Утверждается итоговая смета.
Все перекрытия очищаются от пыли и мельчайших частиц, чтобы обеспечить максимальную адгезию.
В случае необходимости перекрытие ремонтируется: заделываются трещины, удаляются возможные дефекты.
На перекрытия клеятся листы или ламели углепластика, сверху наносится запечатывающий слой.
В случае необходимости можно присыпать всю поверхность кварцевым песком, что даст лучшее сцепление с материалами отделки.
Расчет усиления железобетонных конструкций
Расчет упрочнения железобетонных конструкций (стен, перекрытий, фундаментов, колонн) и иных систем зданий предполагает ответственную и сложную работу, которая может быть выполнена исключительно профессионалами высокой квалификации. Самостоятельно выполнять расчеты не рекомендуется однозначно. Обычно задачу поручают целым отделам проектных организаций – отыскать специалистов в пределах Москвы и дальних регионов не составит труда.
Какие данные нужны для расчета усиления ЖБ конструкций:
Результаты экспертизы, обследований тех строительных конструкций, что планируется усиливать – без них расчеты осуществить невозможно.
Подробные фото поверхности – очень желательны.
Детальные пояснения, что и как нужно делать.
Обычно расчеты усиления конструкций проводят в течение 1-5 дней, но желательно уточнить, так как срок может зависеть от объемов работ, загруженности специалистов и других не менее важных параметров.
Усиление бетона углеволокном – современный и эффективный метод повышения несущей способности конструкций, устранения последствий аварий, реконструкции старых элементов и упрочнения новых.
Источник
Усиление конструкций углеволокном в Москве, цены на усиление бетона и несущих конструкций
от 1350 руб/м2 Отправить заявку
Усиление конструкций углеволокном – это прогрессивная технология, которая позволяет возвращать конструкциям утраченную несущую способность при помощи армирования специальными усиливающими элементами, изготовленными из композитных материалов.
История применения этого метода в отечественном строительстве достаточно непродолжительна и насчитывает чуть менее двадцати лет. Впервые он был применен всего лишь в 1998 году, однако с тех пор технология серьезно шагнула вперед и, на сегодняшний день, она широко применяется повсеместно. Для того, чтобы усиливать строительные конструкции, используется особо прочное углеволокно. Его наклеивают на элемент, нуждающийся в усилении, тем самым повышая его несущую способность. Для приклеивания используются специальные составы, содержащие эпоксидные смолы и обладающие большим уровнем адгезии, либо минеральные клеи. Углеволокно позволяет усиливать конструкции, при этом не расходуя полезный объем помещения, за счет того, что углеволоконные усиливающие элементы обладают высокими физико-механическими свойствами. Лист, который наклеивается на конструкцию в среднем имеет толщину 1-5 мм, а его небольшой вес позволяет усилить конструкцию без создания дополнительной нагрузки, как это произошло бы в случае использования металлических усиливающих элементов.
Усиление строительных конструкций углеволокном –это один из многих используемых вариантов. Здесь важно помнить, что углеволокно представляет собой лишь материал, а не само изделие, поэтому эффективность принимаемых мер по усилению напрямую зависит не только от свойств самого материала, но и от того, насколько грамотно было проработано расположение армирующих элементов и от, того, какие элементы будут использованы. Их разновидностей много – ленты, ламели, сетки и т.д.
Чаще всего, к усилению углеволокном прибегают на железобетонных конструкциях, что обусловлено невозможностью создания дополнительной незапланированной нагрузки на этот материал. Но также углеволокно активно применяется и когда речь идет о деревянных, железных и кирпичных конструкциях.
Порядок усиления несущих конструкций углеволокном регулируется специальным нормативным документом, который называется «Усиление железобетонных конструкций композитными материалам. Правила проектирования».
Для того, чтобы усиление конструкций было выполнено эффективно, материал должен отвечать определенным требованиям:
- Волокна в структуре материала должны располагаться параллельно
- Чтобы сохранять структуру армирующих элементов, нужно использовать специальную стеклянную сетку
Для того, чтобы материал соответствовал принятым требованиям, он должен изготавливаться в строгом соответствии с производственной технологией, в этом случае, качество материала будет высоким, а комплекс мер по усилению конструкции углеволокном – эффективным.
Правильно изготовленный материал обладает поистине уникальными свойствами. У него совсем небольшой вес, который не создает дополнительной нагрузки на конструкцию по массе, однако, в то же время, даже материал небольшой толщины обладает очень высокой прочностью. Армирующие элементы из углеволокна используются, как при усилении конструкций уже возведенных зданий, так и при строительстве новых.
Преимущества композитных материалов
Усиление несущих конструкций углеволокном – это прогрессивный и современный метод, который обладает целым рядом преимуществ, обусловленных свойствами самого материала:
- Для того, чтобы выполнить работы по усилению, вам не понадобится привлечение специальной техники с большой грузоподъемностью, поскольку материал имеет небольшой вес.
- Технология внешнего армирования железобетонных конструкций с помощью композитных материалов позволяет выполнять эти работы до 10 раз быстрее, чем при использовании других технологий.
- Материал, позволяет добиться четырехкратного увеличения несущей способности конструкции по сравнению с аналогичным показателем при использовании других материалов.
- Нагрузка по массе на конструкцию не становится больше
- Углеволокно не подвержено воздействию коррозийных процессов и негативных факторов внешней среды
- Срок службы материала может составлять более 75 лет
- На сегодняшний день углеволокно – это наименее затратный и наиболее эффективный способ исправления ошибок при проектировании и выполнении предварительных строительных работ
Эффективность данной технологии трудно переоценить. Ее применение помогает избежать серьезных эксплуатационных проблем при повреждении конструкций в результате естественного износа или механических воздействий. Усиление позволит не только минимизировать последствия полученных повреждений, вернув конструкции прежнюю несущую способность, но даже существенно повысить ее. Кроме того, плотный и водонепроницаемый композитный материал защитит бетон от влаги и предотвратит появление коррозии в арматуре.
Этапы работ и виды армирующих элементов
Общий принцип усиления везде одинаков – углеволокно наносится на те участки конструкции, где присутствует наибольшее напряжение. Чаще всего это – центр пролета конструкции по нижней грани. А для решения конкретных задач нужно будет определиться с тем, какой вид армирующих элементов подойдёт лучше всего – ленты, ламели или сетка.
Ленты и ламели
Усиление строительных конструкций лентами и ламелями из углеволокна происходит сходным образом. Для этого применяются одинаковые или схожие адгезивы, а монтаж осуществляется по общим принципам. Именно поэтому их часто используют в совокупности.
Применение углеродной сетки практически в ста процентах случаев исключает возможность использования ленты и ламелей, поскольку ее монтаж сопряжен с выполнением «мокрых» работ.
Как происходит выполнение работ?
Изначально, главное, что необходимо сделать –это определить те самые участки конструкции, которые испытывают наибольшие нагрузки, а, следовательно, нуждаются в усилении. После этого происходит разметка конструкции и начинаются подготовительные работ, в ходе которых, участки, на которые будет наклеиваться композит тщательно очищают от отделки, грязи и т.д. Очистка происходит с применением специального шлифовочного оборудования.
Шлифовка
То, насколько хорошо подготовлена была поверхность бетона к наклеиванию композитного усиления, напрямую влияет на его эффективность, поскольку от этого зависит совместная работа бетона и композита по распределению нагрузки. Шлифовка должна осуществляться с соблюдением технологии. Полностью должно быть исключено попадание влаги на шлифуемую поверхность, а также после шлифовки следует полностью удалить пыль и грязь.
Компоненты
После того, как была подготовлена поверхность усиливаемой бетонной конструкции, настает очередь подготовки армирующих компонентов. Углеволокно поставляется в заводской упаковке в скатанном виде. Для того, чтобы начать работать с материалом, подготовьте для этого специальную зону на строительной площадке, застеленную полиэтиленом. Делается это для того, чтобы исключить попадание бетонной пыли на материал, поскольку это приведет к браку. Нарезать углеродное полотно можно при помощи обычного строительного ножа, ножниц по металлу. Отрезка ламелей может быть осуществлена при помощи угол-шлифовальной машинки.
Для наклейки чаще всего используют двухкомпонентные клеящие составы. Приобрести ингредиенты не составит труда, но следует строго соблюдать инструкции производителя при их смешивании, четко рассчитывать дозировку с помощью весов. Проблемы с этим возникнуть не должно, поскольку многие современные поставщики строительных адгезивов предлагают их уже упакованными в специальные ведра. Добавляйте адгезив постепенно, чтобы предотвратить его закипание в процессе смешивания компонентов.
Монтаж
Монтаж углеродной ленты производится «сухим» или «мокрым» методом. Разница между ними заключается в том, в первом случае ленту сначала прикладывают к основанию, после чего пропитывают адгезивом, а втором случае пропитка происходит сначала. Состав тщательно наносят на поверхность армирующего компонента таким образом, чтобы об проник вглубь материала и вышел наружу со стороны бетонного основания. Ламели монтируются схожим образом, только связующий состав в этом случае наносится и на основание, и на сам элемент. А углеродная сетка всегда монтируется на слегка увлажненную поверхность бетонного основания.
Если вам нужна консультация…
Рассказать в рамках одной статьи все тонкости выполнения работ по усилению конструкций углеволокном не представляется возможным – настолько обширна эта технология. Однако, если на вашем объекте возникла необходимость выполнения эти работ, вы всегда можете обратиться в компанию «ПРАЙМ».
Мы будем рады проконсультировать вас по любым вопросам, а также произвести любые работы по усилению конструкций композитом. У нас имеется обширный опыт работы на объектах любых масштабов и любого профиля!
Усиление конструкций углеволокном – цены в Москве – РусКомпозит
Оглавление страницы
- 1.Когда применяют
- 2.Преимущества
- 3.Цены
Физико-механические свойства углеволокна позволяют значительно повысить несущую способность любой конструкции без увеличения веса сооружения и потери полезной площади помещений: толщина усиливающего материала составляет всего 1-5 мм. Зачастую усиление углеволокном используют для железобетонных сооружений, но технология применима и для укрепления построек из дерева, металла или камня.
Наша компания занимается производством и продажей качественного углеволокна. Мы также оказываем услуги по расчету количества необходимых материалов для определенных потребностей заказчика. По вашему запросу, наши менеджеры подберут композиты, оптимально подходящие для конкретного случая. Если вам необходимо усиление конструкций углеволокном, звоните по телефону на сайте и наш технический эксперт проконсультирует вас по всем интересующим вопросам!
Преимущества использования углеволокна
Защита материала от механических повреждений, деформации.
Усиление ж/б конструкций углеволокном не мешает стройке или использованию уже готового здания. Из эксплуатации выводят лишь участок реконструкции.
Не нужно переделывать строительный проект или вносить изменения в первоначальный план сооружения.
Благодаря гибкости материала им можно укреплять конструкции даже сложных архитектурных форм.
Углеродному волокну не грозит коррозия, его можно применять даже в условиях высокой влажности.
Простота работ, экономия. Для монтажа материала не нужно использовать сложную технику или большое количество человеческих ресурсов, кроме того, стоимость самого углеволокна относительно невысокая.
Композиты из углеволокна в 10 раз легче аналогичных материалов из бетона или металла. Это позволяет использовать их там, где увеличение массы конструкции критически опасно.
Усиление бетона углеволокном гарантирует более высокую прочность сооружения, чем усиление металлом. При этом, прочностные характеристики распространяются на растягивание, упругость, изгибание, разрыв и все другие параметры усиления.
Материал невосприимчив к агрессивным веществам: его используют на объектах химической промышленности, производствах газа и нефти.
В зависимости от типа сооружения и материала несущих элементов, наши специалисты подберут для вас подходящие материалы в нужном количестве. Кроме того, мы предлагаем своим клиентам выгодную цену на усиление железобетонных конструкций углеволокном.
Наши квалифицированные и опытные инженеры ответят на все ваши вопросы и предоставят рекомендации по проекту. Для этого звоните по номеру: +7 499 348 82 52
Сколько стоит обследование, проектирование и усиление углеродным волокном
Вид объекта | Срок выполнения работы (в днях) | Объём работ | Цена за единицу | Метод укрепления |
Проёмы и отверстия | 5 | от 1 до 50 шт. | от 9 000 до 25 000 руб/шт. | Использование углепластика, карбоновых лент, сеток, ламелей. |
Усиление перекрытий и покрытий | 5-8 | от 100 кв.метр | от 340 до 4 400 руб/кв.метр | Обустройство углеволоконных ламелей, сетки, ленты. Монтаж металлоконструкций. |
Стены и пилоны | 7-10 | от 100 до 5 000 кв.метр | от 500 до 3 700 руб/кв.![]() | Укрепление углеволокном. |
Ригели/балки | 3-5 | от 100 пог.м | от 410 до 4 600 руб/пог.м | Наращивание сечений, обустройство сеток и ламелей из углеволокна. |
Железобетонные фермы | от 100 пог.м | индивидуальный расчёт | по договору | Укрепление растягиванием арматурой, наращиванием сечений. |
Колонны | 5-7 | от 100 до 5 000 кв.метр | от 500 до 4 500 руб/пог.м | Создание стальных обойм, применение композитных материалов. |
Усиление углеволокном конструкций зданий: цена в Москве
Наша компания выполняет усиление строительных конструкций, промышленных, коммерческих комплексов и сооружений углеродным волокном. Это современный композитный материал на основе карбона. Выпускается он в виде холста, ленты, сетки; подходит для укрепления внутренних или внешних элементов здания: плит, несущих колонн, арок. Компания сертифицирована, имеет необходимые допуски. Выезд на объект — по Москве и Московской области. Стоимость армирования композитной тканью — в прайс-листе на сайте.
Когда необходимо укрепление углеродным холстом
Мы проводим усиление ж/б конструкций углеволокном с применением неразрушающих технологий. Подрядчик выполняет работы по армированию:
- В ходе реконструкции, перепланировки, генерального ремонта. Компания выявляет слабые участки, для укрепления использует листы углеродного волокна соответствующей геометрии.
- После долгой эксплуатации здания. При использовании торгового или производственного комплекса, жилого здания неизбежно снижаются прочностные характеристики бетона. Армирование композитным холстом помогает предотвратить разрушение сооружений.
- При выявлении ошибок проектирования или строительства. Неправильно проведённый прочностной расчёт приводит к быстрому падению характеристик бетона. Метод армирования углеродной тканью позволяет исправить допущенные строителями недочёты, локально увеличить прочность конструкций.
- После аварий, пожаров, сильных повреждений здания. Усиление конструкций углеволокном поможет предотвратить окончательное разрушение, быстрее восстановить работоспособность объекта.
Получите оценку объекта и расчет коммерческого предложения
Современная технология против устаревших методов усиления
Углеродный холст — высокопрочный, нетоксичный, эластичный полимерный материал. Армирование, проведённое углехолстом, способно заменить традиционные способы укрепления в строительстве:
- Торкретирование. На поверхность повреждённой колонны, стены или плиты наносится новый слой бетона, что приводит к изменению массогабаритов элемента.
- Инъектирование. Внутрь плиты, перекрытия, фундамента под давлением вводится быстросхватывающийся ремонтный раствор. Такой метод также связан с утяжелением усиливаемых зданий.
- Внешнее армирование, установка дополнительных поддерживающих элементов.
Отнимают жизненное пространство, трудны в исполнении, часто требуют предварительного разрушения старых элементов.
Усиление железобетонных конструкций композитным волокном, выполняемое нашей компанией, лишено перечисленных недостатков. Цена материала позволяет заменить углехолстом любой из этих способов — и завершить работу значительно быстрее.
Преимущества армирования углеволокном
Полимерный высокомолекулярный материал, укрепление которым мы предлагаем, имеет принципиальные преимущества:
- Малый вес. Карбоновое волокно тонко, легко, практически не изменяет массогабариты укрепляемого элемента.
- Гибкость. Материал легко гнётся, после высыхания сохраняет пластичность. Может использоваться на поверхностях сложной геометрии.
- Химическая инертность. Усиление углеволокном можно применять в агрессивных средах, в условиях обильных осадков. Материал не ржавеет, не разъедается кислотными или щелочными соединениями.
- Простота крепления.
Чтобы выполнить армирование карбоновой тканью, не придётся останавливать производство, выводить людей из всего здания. Укрепление проводится быстро, может быть выполнено одним-двумя работниками.
- Огромный запас прочности. Композитная ткань показывает лучшие характеристики на скручивание, растяжение, изгиб, разрыв, чем сталь.
- Доступность. Стоимость углеволокна даёт возможность полностью заменить им устаревшие методы армирования.
Цены на
усиление углеволокном
Колонны | от 3000 руб/м² |
Стены и пилоны | от 3000 руб/м² |
Балки и ригели | от 74 000 руб/т |
Покрытия и перекрытия | от 7000 руб/м² |
Проёмы и отверстия | от 2800 руб/м² |
Ж/б фермы | от 3000 руб/м² |
Полимер, армированный углеродным волокном — обзор
10.
3.1 Механизмы поглощения энергии в композитных конструктивных элементах
Хотя углепластик, как правило, является хрупким при растяжении с низкими деформациями разрушения, было показано, что композитные структурные элементы разрушаются при других режимах разрушения такие как местное сжатие, сдвиг, микровыступ или расслоение, обладают способностью поглощать энергию за счет контролируемого прогрессирующего разрушения из-за раздавливания. Ключевым моментом является запуск режима постепенного разрушения, при котором поглощенная энергия значительно выше, чем измеренная при хрупких отказах.Это достигается с помощью спусковых механизмов (также известных как инициаторы разрушения), введенных в структурный элемент, которые уменьшают пиковые силы разрушения и вызывают режим прогрессирующего разрушения, распространяющийся через конструкцию. Наблюдалось множество различных режимов прогрессирующего разрушения, которые в значительной степени зависят от типа волокна, типа матрицы, границы раздела волокно-матрица, последовательности укладки волокон и ориентации волокон, геометрии образца, режима нагрузки, конструкции триггера, скорости деформации, температурных эффектов и т. Д. Энергопоглощающие виды отказов продолжаются более 30 лет, охватывая все аспекты от микромеханики композитов до макромеханики на уровне слоев / ламината, до запуска концепций и проектирования на структурном уровне.
Ранняя работа [32–37] показала, что стеклянные или углепластиковые трубки, нагруженные при осевом сжатии через скошенный или скошенный конец трубки (спусковой механизм снятия фаски), могут выйти из строя в режиме постепенного раздавливания при условии, что толщина стенки трубки достаточно высока для предотвращения преждевременного глобальные или локальные отказы продольного изгиба. В ходе этой работы основные механизмы разрушения были идентифицированы как режим расширения или фрагментации. Расщепление начинается при спуске фаски из-за расслоения на фронте раздавливания, которое вызывает изгиб или растяжение слоев наружу, что приводит к осевому расщеплению и изгибу или разрушениям при поперечном сдвиге.В зависимости от пластичности композита расширенные слои или листья будут короткими из-за фрагментации или длинными. Фрагментация более коротких пластин на фронте раздавливания приводит к образованию клина обломков, который затем вызывает отказы расслоения и приводит к устойчивому режиму отказов при раздавливании с высоким EA. Это основной механизм композитных трубчатых поглотителей при осевых сжимающих нагрузках. Важным шагом в разработке ударопрочных композитных структур было показать, что аналогичные механизмы разрушения могут запускаться в нетубулярных структурных элементах, таких как открытые круглые сегменты и синусоидальные сети [27,36] и коробчатые секции [38].
Для измерения и понимания ЭА и механизмов отказа композитных структурных элементов требуется разработка новых процедур испытаний и соответствующих образцов для испытаний. Фераболи [9] рассматривает существующие процедуры испытаний и обсуждает характеристики плоских пластин и гофрированных образцов для испытаний на осевое раздавливание. Характеристики EA, которые необходимо измерить, получены для образцов, которые выходят из строя в устойчивом режиме раздавливания, для чего требуются специально разработанные опорные приспособления или самонесущие образцы, такие как трубы и цилиндрические профили. Компания DLR разработала образцы сегментов труб с фаской, см. [28], которые легче изготовить, чем трубки, они самостабилизируются без боковых опор и дают воспроизводимые разрушения при осевом раздавливании как в условиях квазистатического, так и динамического нагружения. Квазистатические испытания образцов сегментов трубы со скошенной фаской обсуждаются здесь, а динамические испытания на раздавливание описаны далее в [39]. Образцы для испытаний состоят из полукруглого цилиндрического сегмента с фланцами на продольных свободных краях для предотвращения местного коробления при осевом сжатии.Они были изготовлены из углеродной ткани Hexply M18 / 1/43% / G939-220gsm 4HS / эпоксидного препрега с восемью слоями ткани и слоем [0/90/0/90]. Размеры: длина 75 мм, диаметр по фланцам 50 мм, номинальная толщина 2,0 мм. Спусковой механизм имел внешнюю фаску под углом 45 °, что инициировало устойчивый процесс дробления на кончике фаски. Основание сегментных образцов закреплено в опорном зажиме на нижней стальной плите, установленной на датчике нагрузки квазистатической испытательной машины.
Кромка с фаской подвергается осевому сжатию стальной пластиной, прикрепленной к траверсе, которая нагружает образец со скоростью 1 мм / с.Время осевого усилия и время смещения крейцкопфа измеряются в испытании для типичных расстояний раздавливания 50 мм.
На рис. 10.4 показаны изображения пленки испытания на раздавливание, показывающие три фазы: раздавливание спускового крючка, растяжение ламината на внутреннюю и внешнюю пластинки с центральной трещиной расслоения с последующим осевым расщеплением пучков пластинок на лепестковидные ветви. как более подробно описано в [40] и видно на окончательном раздавленном образце на Рисунке 10.5 (а). Стационарная фаза раздавливания состоит из образования вайя, вызванного центральной трещиной расслоения с клином обломков, рис.10.5 (b), на котором показано рентгеновское сканирование с помощью компьютерной томографии высокого разрешения (HRCT) поперечного сечения стенки сегмента на фронте раздавливания. Измеренная кривая сдавливающего усилия-смещения сегментного образца показана на рис. 10.6 до смещения 40 мм. Кривая показывает быстро возрастающую нагрузку с пиком при смещении примерно 2 мм, что соответствует нагрузке на спусковой механизм снятия фаски. За этим следует резкое падение нагрузки, поскольку спусковой механизм срабатывает, и нагрузка падает до постоянного среднего значения в установившейся фазе дробления.Это постоянное раздавливание является основным механизмом, используемым при разработке энергопоглощающих структур композитов. Ключевыми параметрами для проектирования таких устройств являются установившаяся сила раздавливания (SSCF), EA, определяемая как площадь под кривой силы сжатия-смещения, и SEA, которая представляет собой энергию, поглощенную на единицу массы разрушенного материала. Эти данные показаны в первой строке таблицы 10.1 с SSCF 24 кН и SEA 87,1 кДж / кг, которые являются типичными значениями для квазистатических испытаний сегментов DLR с материалами препрега из углеродной ткани M18 / 1.В расширенном исследовании этих образцов с различными слоями ламината и вариантами изготовления сообщается в [41]; диапазон SEA 79,4–90,6 кДж / кг был измерен при изменении укладки с различными пропорциями слоев ткани под углом 0 ° и 45 ° к оси нагрузки.
Рисунок 10.4. Последовательность квазистатических испытаний на раздавливание сегмента трубы из углеродной ткани / эпоксидной смолы.
Рисунок 10.5. Образец сегмента углеродной ткани / эпоксидной смолы после квазистатического испытания на раздавливание. а) раздробленный сегмент; (b) Компьютерная томография высокого разрешения фронта разрушения.
Рисунок 10.6. Кривые сдавливающего усилия для образцов сегмента углеродной ткани / эпоксидной смолы при различных скоростях нагружения.
Таблица 10.1. Характеристики поглощения энергии сегментов из армированного углеродным волокном полимера при различных скоростях нагружения
Скорость нагружения (м / с) | Пиковая сила сжатия (кН) | SSCF (кН) | Расстояние раздавливания (мм) | Поглощенная энергия (кДж) | SEA (кДж / кг) |
---|---|---|---|---|---|
0.001 | 31,86 | 24,03 | 58,48 | 1,420 | 87,11 |
2,00 | 31,01 | 17,71 | 49,29 | 0,891 | 67,89 |
5,00 | 27,88 | 0,825 | 67,53 | ||
10,00 | 35,69 | 18,04 | 41,62 | 0,741 | 67,04 |
Рисунок 10. 6 также представлены эквивалентные кривые «сила-перемещение» на образцах аналогичных сегментов, испытанных динамически при более высоких скоростях нагружения при скоростях 2 м / с, 5 м / с и 10 м / с на испытательной машине Instron VHS 100/20 с высокой скоростью деформации в DLR. см. подробности в [39]. Это показывает, что динамические образцы показали устойчивую реакцию на раздавливание после запуска при начальной пиковой нагрузке. Наиболее интересной особенностью кривых является то, что три динамические кривые были очень похожи, без явной зависимости от скорости испытания, и все они были значительно ниже квазистатической кривой испытания.В таблице 10.1 приведены основные результаты квазистатических и динамических испытаний. Это показывает снижение на 22% в SEA и на 26% в SSCF при 2 м / с по сравнению с квазистатическими значениями. Эти результаты согласуются с предыдущими испытаниями, проведенными в DLR на ударных элементах, и объясняются более хрупким поведением композита при более высоких скоростях, что приводит к более коротким слоям на фронте раздавливания, которые быстрее фрагментируются, поглощая меньше энергии.
Эти данные важны для проектировщика, поскольку композитные амортизаторы рассчитаны на ударные нагрузки, и очевидно, что использование квазистатических испытаний для разработки структур EA неконсервативно.
Сегменты полутруб со скошенными кромками демонстрируют высокую УЭА, но сами по себе не подходят в качестве структурных поглотителей энергии из-за своей идеальной формы. Испытания на раздавливание сегментов относительно легко выполнить с высокой воспроизводимостью, и эти испытания в основном используются для проверки новых композитных материалов и слоев для использования в амортизаторах энергии столкновения. Они являются основным элементом синусоидальной волны и гофрированных полотен, которые используются в прочных конструкциях чернового пола, как описано в [27,36]. Текущий интерес сейчас заключается в изучении поведения EA для ряда составных форм каналов, которые затем могут стать основой более продвинутых структур EA.Детальное исследование профилей из углеродной ткани / эпоксидной смолы с гофрированными полотнами [9] и нескольких секций каналов, вырезанных из коробчатых секций, включая полную коробку, C-образные каналы и прямоугольные угловые секции [42], было проведено в CMH-17. Группа [8]. Квазистатические испытания секций канала, изготовленных из тканого препрега Toray T700 / 2510, показали значения SEA в диапазоне от 80 кДж / кг для гофрированного полотна, 62 кДж / кг для небольшого прямоугольного углового участка и до 37 кДж / кг для коробчатого сечения и большого С-образного канала.Это следует из различных видов отказов, зависящих от формы. Гофрированное полотно разрушалось подобно сегментам DLR и имело высокий SEA, тогда как в С-образном канале неподдерживаемые боковые стенки изгибались наружу и вызывали общий режим отказа с расширением с поглощением энергии за счет разрыва по углам канала.
Чтобы повысить уровень сложности, CRC-ACS исследовали различные интегрированные композитные структуры, включающие круглые и трапециевидные сегменты, прикрепленные и / приклепанные к опорным пластинам или используемые в качестве сердечника с многослойной обшивкой, как сообщалось в [29, 43–45].Эти тестовые статьи были разработаны для получения информации об эффекте интеграции элементов раздавливания с окружающей структурой. Были проведены испытания, чтобы изучить разницу между скрепленными и механически скрепленными компонентами, а также влияние различных путей приложения нагрузки. Это привело к развитию веб-сегмента EA, который обсуждается далее в Разделе 10.3.3 и является основным элементом концептуальной структуры пола, описанной в Разделе 10.4.
Что такое композиты CRFP и почему они полезны?
Полимерные композиты, армированные углеродным волокном (CFRP), представляют собой легкие и прочные материалы, используемые в производстве многочисленных продуктов, используемых в нашей повседневной жизни.Это термин, используемый для описания армированного волокном композитного материала, в котором углеродное волокно используется в качестве основного структурного компонента. Следует отметить, что буква «P» в углепластике может также обозначать «пластик», а не «полимер».
Как правило, в композитах из углепластика используются термореактивные смолы, такие как эпоксидная смола, полиэфир или винилэфир. Хотя термопластические смолы используются в композитах из углепластика, «термопластичные композиты, армированные углеродным волокном» часто называют их собственным акронимом — композиты из углепластика.
При работе с композитами или в производстве композитов важно понимать термины и сокращения.Что еще более важно, необходимо понимать свойства композитов FRP и возможности различных армирующих материалов, таких как углеродное волокно.
Свойства композитов из углепластика
Композитные материалы, армированные углеродным волокном, отличаются от других композитов FRP, в которых используются традиционные материалы, такие как стекловолокно или арамидное волокно. К преимуществам композитов из углепластика относятся:
Легкий вес: Традиционный композит, армированный стекловолокном, использующий непрерывное стекловолокно с содержанием стекла 70% (вес стекла / общий вес), обычно будет иметь плотность.065 фунтов на кубический дюйм.
Между тем, композит CFRP с тем же весом волокна 70% обычно может иметь плотность 0,055 фунта на кубический дюйм.
Повышенная прочность: Не только композиты из углеродного волокна легче, но и композиты из углепластика намного прочнее и жестче на единицу веса. Это верно при сравнении композитов из углеродного волокна со стекловолокном, но даже в большей степени по сравнению с металлами.
Например, неплохое практическое правило при сравнении стали с композитами из углепластика состоит в том, что структура из углеродного волокна с одинаковой прочностью часто будет весить 1/5 от веса стали.Вы можете себе представить, почему автомобильные компании исследуют использование углеродного волокна вместо стали.
При сравнении композитов из углепластика с алюминием, одним из самых легких используемых металлов, стандартное предположение состоит в том, что алюминиевая структура равной прочности, вероятно, будет весить в 1,5 раза больше, чем структура из углеродного волокна.
Конечно, есть много переменных, которые могут изменить это сравнение. Сорт и качество материалов могут быть разными, и в случае композитов необходимо учитывать производственный процесс, архитектуру волокна и качество.
Недостатки композитов углепластика
Стоимость: Несмотря на то, что это замечательный материал, есть причина, по которой углеродное волокно не используется во всех сферах применения. В настоящее время композиты из углепластика во многих случаях являются дорогостоящими. В зависимости от текущих рыночных условий (спрос и предложение), типа углеродного волокна (аэрокосмический или коммерческий) и размера жгута волокна цена на углеродное волокно может сильно различаться.
Необработанное углеродное волокно по цене за фунт может быть в 5-25 раз дороже, чем стекловолокно.Это несоответствие еще больше при сравнении стали с композитами из углепластика.
Электропроводность: Это может быть как преимуществом композитов из углеродного волокна, так и недостатком в зависимости от области применения. Углеродное волокно обладает высокой проводимостью, а стекловолокно — изоляционными. Многие приложения используют стекловолокно и не могут использовать углеродное волокно или металл строго из-за проводимости.
Например, в коммунальной промышленности требуется, чтобы во многих продуктах использовалось стекловолокно.Это также одна из причин, почему в качестве перил лестниц используется стекловолокно. Если лестница из стекловолокна соприкоснется с линией электропередачи, вероятность поражения электрическим током будет намного ниже. Это не относится к лестнице из углепластика.
Хотя стоимость композитов из углепластика по-прежнему остается высокой, новые технологические достижения в производстве продолжают обеспечивать возможность создания более рентабельных продуктов. Надеюсь, что в течение нашей жизни мы сможем увидеть экономичное углеродное волокно, используемое в широком спектре потребительских, промышленных и автомобильных приложений.
Рост производства пластмасс, армированных углеродным волокном
Углеродные волокна в пластмассах
Использование углеродных волокон в пластмассах имеет долгую историю. Еще в 1879 году Томас Эдисон экспериментировал с углеродными волокнами, сделанными из хлопковых нитей и бамбуковых лент. Фактически, первая лампа накаливания, нагретая электричеством, содержала углеродные волокна.
В 1960-х годах доктор Акио Шиндо из Агентства промышленных наук и технологий Японии разработал углеродное волокно на основе полиакрилонитрила (PAN).Полученное волокно содержало 55% углерода.
Процесс преобразования на основе PAN быстро стал основным методом производства углеродного волокна. Сегодня 90% углеродных волокон изготовлены из полиакрилонитрила (C 3 H 3 N) n или синтетической полукристаллической органической полимерной смолы PAN. Остальные 10% произведены из искусственного волокна или нефтяного пека. Волокна из PAN очень прочные и легкие. Эти волокна связаны термореактивными или термопластичными полимерами, такими как полиэфир, сложный виниловый эфир или нейлон, для изготовления пластика, армированного углеродным волокном, или углеродного FRP.
Добавление углеродного волокна в полимер имеет много преимуществ
Увеличиваются прочность на разрыв и модуль упругости при изгибе, как и температура теплового прогиба или HDT. Кроме того, добавление армирования углеродным волокном уменьшает усадку и коробление.
Каждое углеродное волокно представляет собой длинную тонкую нить, состоящую из тысяч углеродных нитей. Одно волокно имеет диаметр около 5-10 мкм и состоит в основном из углерода. Микроскопические кристаллы в углероде связываются вместе в структуре, которая более или менее выровнена параллельно длинной оси волокна.Именно это расположение кристаллов делает волокна такими прочными.
Классификация по модулю упругости
Углеродные волокна классифицируются по модулю упругости волокна * . Модуль упругости при растяжении может находиться в диапазоне от 34,8 миллионов фунтов на квадратный дюйм до 72,5-145,0 миллионов фунтов на квадратный дюйм. Сталь имеет модуль упругости 29 миллионов фунтов на квадратный дюйм, поэтому самое прочное углеродное волокно в пять раз прочнее стали.
Волокна
с «низким» модулем упругости имеют модуль упругости ниже 34,8 миллиона фунтов на квадратный дюйм (240 миллионов кПа). Волокна также классифицируются в порядке возрастания модуля упругости при растяжении: «стандартный модуль», «промежуточный модуль», «высокий модуль» и «сверхвысокий модуль». Углеродные волокна с классом сверхвысокого модуля упругости имеют модуль упругости 72,5–145,0 миллионов фунтов на квадратный дюйм (500–1,0 миллиарда кПа).
Прядение, стабилизация, карбонизация, обработка поверхности и калибровка
Процесс производства углеродного волокна частично химический, а частично механический.
- Прядение: PAN прядется с использованием одного из нескольких процессов прядения.Этот шаг важен, потому что он формирует внутреннюю атомную структуру волокна. Затем волокна промываются и растягиваются до необходимого диаметра. Растяжение также помогает выровнять молекулы, способствуя образованию кристаллов углерода, созданных карбонизацией.
- Стабилизация: На этом этапе волокна обрабатываются химикатами, чтобы изменить их линейное соединение на термостойкую структуру лестничного соединения.
Затем нити нагреваются на воздухе, так что они захватывают молекулы кислорода и меняют структуру их атомных связей.
- Карбонизация: Затем волокна подвергаются очень сильному нагреву без присутствия кислорода, поэтому волокно не может гореть. Атомы в волокне сильно колеблются, вытесняя большинство неуглеродных атомов в предшественнике.
- Обработка поверхности: После карбонизации поверхность волокон плохо сцепляется с материалами, используемыми для изготовления композитных материалов. На этом этапе поверхность волокон слегка окисляется путем погружения в различные газы или жидкости.
- Проклейка: В этом процессе волокна покрываются покрытием, чтобы защитить их от повреждений во время намотки или ткачества.
Некоторые изделия из углеродного волокна включают удочки, велосипеды, снаряжение для гольфа, теннисные ракетки, детали для самолетов, мостов и автомобилей.
* Модуль упругости — это то, сколько тянущего усилия волокно определенного диаметра может проявить без разрушения. Модуль упругости выражается в фунтах на квадратный дюйм или фунтах на квадратный дюйм.
Вопросы? Дайте мне знать в разделе комментариев ниже.
Ищете дополнительную информацию о пластмассах? Загрузите наше бесплатное руководство!
Полимеры, армированные углеродным волокном, для бетонных конструкций
🕑 Время чтения: 1 минута
Углерод
армированный волокном полимер (CFRP) — это тип композитных материалов, состоящих из
углеродное волокно и полимер. Углеродное волокно обеспечивает прочность и жесткость
в то время как полимер действует как связная матрица для защиты и удержания волокон
вместе. Углепластик изготавливается в виде полос, стержней и листов с использованием различных
технология производства, такая как намотка филамента, пултрузия и ручная укладка
процессы.
углепластик
материалы обладают хорошей жесткостью, высокой прочностью, малой плотностью, коррозии
сопротивление, вибростойкость, высокая предельная деформация, высокая усталость
сопротивление и низкая теплопроводность. Они плохие проводники
электричество и немагнитны.
Углепластик обеспечивает решение многих проблем, связанных с износом и
укрепление инфраструктуры, такой как мосты и здания. Использование углепластика
арматурные стержни в новом бетоне могут устранить потенциальные проблемы с коррозией и
существенно увеличить структурную прочность элемента.
эффективный
использование полимера, армированного углеродным волокном, может значительно продлить срок службы
конструкции, минимизирующие требования к обслуживанию. Углеродные волокна также имеют
использовался в качестве усиления для абляционных пластиков и для усиления для
легкие, высокопрочные и жесткие конструкции.
Недвижимость
из углепластика
- Устойчив к щелочам.
- Коррозионная стойкость, поэтому используется для контроля коррозии и восстановления железобетонных конструкций.
- Обладает низкой теплопроводностью.
- Углепластик имеет высокое отношение прочности к массе и, следовательно, исключает необходимость использования тяжелого строительного оборудования и опорных конструкций.
- Требуется короткое время отверждения. Таким образом, приложение занимает меньше времени. Это значительно сокращает продолжительность проекта и время простоя конструкции.
- Углепластик обладает высокой предельной деформацией.
- Высокая усталостная прочность. Таким образом, они не разлагаются, что легко устраняет необходимость частого обслуживания.
- Углепластик плохо проводит электричество и не обладает магнитными свойствами.
- Благодаря легкости сборные компоненты из углепластика можно легко транспортировать. Таким образом, это стимулирует строительство из сборных элементов, снижает затраты на рабочую силу и потребность в капитальных вложениях.
Рис.1: Полосы, листы и стержни из углепластика
Применение углепластика в бетонных конструкциях
1. Полосы углепластика
Есть много методов, использующих углепластик.
полосы, ламинаты для усиления бетонных конструкций, например, для наружного склеивания
Листы из углепластика и стеклопластик, монтируемый на поверхности. Выполнение методов упрочнения
зависит от прочности клея, используемого для приклеивания углепластика к бетону
поверхность и степень напряжения на границе раздела бетона и углепластика.
Углепластик
используется для упрочнения стали.
автомобильные мосты проще и дешевле. Полосы углепластика составляют только 20%
вес полос аналогичных изделий из высокопрочной стали, но
как минимум в четыре раза сильнее. Их высокое соотношение прочности и веса делает
Полосы углепластика просты в обращении и сокращают затраты на установку.Полосы углепластика
толщиной всего 8 мм были использованы для усиления автодорожного моста в
Рочдейл, Великобритания.
Рис.2: Полосы углепластика, используемые для усиления железобетонной плиты
2. Обертки из углепластика
Обертка из углепластика
используется для
восстановление кладки колонн. Обертки из углепластика используются для контроля коррозии.
и восстановление железобетонных колонн. Они также используются для
строительство сейсмостойких конструкций.
Добавление листов углепластика значительно
увеличивает предельный изгибающий момент модернизированной стены, работающей на сдвиг.Однако для того, чтобы лист FRP выдерживал высокие осевые нагрузки, возникающие в результате
от изгибающего момента, приложенного к стенке сдвига, листы углепластика должны быть
надежно закреплен у основания стены.
Рис. 3: Обертывание колонн RC листами углепластика
3.
Ламинат углепластика
Ламинат из углепластика с низким тепловым расширением
используются для усиления конструктивных элементов, таких как балки в зданиях и
балки в мостах. Углепластик используется для более быстрого укрепления стальных дорожных мостов,
дешево и легко.
4. Стержни углепластика
стержня из углепластика находились в стадии строительства.
строительства новостроек и усиления железобетонных конструкций с помощью Near Surface
смонтированная техника армирования углепластика.
Рис.4: Применение стержней из углепластика в железобетонных элементах
Производство
Методы для углепластика
- Непрерывный процесс армирования
- Намотка нитью
- Пултрузия
- Процессы ручной укладки
- Процессы формования
- Формование в согласованных штампах
- Формование в автоклаве
- Вакуумное формование
- Процессы литья под давлением 9019 9019 Литье смолы 9019 литье под давлением
Углеродное волокно, Dupont KEVLAR и стекловолокно
Углеродное волокно, стекловолокно и кевлар®: правильный выбор
Фото предоставлено IStock Photo. Физические свойства композитов — преобладающие волокна. Это означает, что при объединении смолы и волокна их характеристики больше всего соответствуют свойствам отдельных волокон. Данные испытаний показывают, что волокнистая арматура является компонентом, несущим большую часть нагрузки. По этой причине выбор ткани имеет решающее значение при проектировании композитных конструкций.
Начните процесс с определения типа арматуры, необходимой в проекте. Среднестатистический производитель может выбрать один из трех распространенных армирующих материалов: стекловолокно, углеродное волокно и кевлар®.Стекловолокно, как правило, является универсальным выбором, в то время как углеродное волокно обеспечивает высокую жесткость, а кевлар® — высокую стойкость к истиранию. В наш обновленный технический документ «Основы стекловолокна» для справки включена дополнительная информация о выборе ткани. Заказчикам, которым требуется конкретная информация о тестировании, следует обратиться к нашей сравнительной таблице ламината. Эта таблица должна помочь вам выбрать подходящий материал, когда нагрузка на детали известна заранее. Имейте в виду, что в ламинате можно комбинировать разные типы тканей, образуя гибридную укладку с преимуществами более чем одного типа материала.
После того, как семейство ткани определено, выберите вес и стиль переплетения, которые соответствуют требованиям работы. Чем легче унция ткани, тем легче будет драпироваться на поверхностях с сильно очерченными контурами. Легкие также используют меньше смолы, поэтому весь ламинат остается легче. По мере того как ткань становится тяжелее, она становится менее гибкой. Средние веса сохраняют достаточную гибкость, чтобы драпировать большинство контуров, и они вносят значительный вклад в прочность детали (6-, 7.Ткани весом 5 и 10 унций являются нашими самыми популярными). Они очень экономичны и производят прочные и легкие детали, используемые в автомобильной, морской и промышленной сферах. Тканый ровинг является самым тяжелым армированием и обычно используется при строительстве лодок и пресс-форм.
Узор или стиль ткани определяется способом изготовления ткани. Выберите один из трех распространенных стилей переплетения: полотняное, атласное и саржевое. Плетение полотняного переплетения является наименее дорогим и наименее податливым, но оно хорошо держится в разрезе.Частое пересечение нитей снизу или сверху снижает прочность полотняного переплетения, хотя они по-прежнему подходят для всех областей применения, кроме наиболее эффективных.
Атласное и саржевое переплетение очень гибкое и прочнее, чем полотняное переплетение. В атласном переплетении одна пряжа наполнителя плавает над тремя-семью другими нитями основы, прежде чем прошиваться под другим волокном основы. Нити этого типа с неплотным плетением идут ровнее и дольше, сохраняя теоретическую прочность волокна.Саржевое переплетение — это компромисс между атласным и однотонным стилем, а также часто желаемый косметический эффект в виде елочки.
Технический совет:
Чтобы повысить податливость любой ткани, отрежьте ее от рулона под углом 45 градусов. При таком раскрое даже самая грубая ткань будет лучше драпироваться по контуру.
Стекловолокно — основа композитной промышленности. Он используется во многих приложениях для композитов с 1950-х годов, и его физические свойства довольно хорошо изучены.Стекловолокно легкое, имеет умеренную прочность на растяжение и сжатие, устойчиво к повреждениям и циклическим нагрузкам, а также с ним легко обращаться.
Стекловолокно — наиболее широко используемый из всех доступных композитных материалов. В основном это связано с его относительно низкой стоимостью и умеренными физическими свойствами. Стекловолокно идеально подходит для повседневных проектов и деталей, которые не требуют дополнительной прочности и долговечности по сравнению с более дорогими тканями.
Технический совет:
Чтобы максимизировать прочностные свойства стекловолокна, его следует использовать с эпоксидной смолой, и он может быть отвержден с использованием стандартных методов ламинирования (никаких специальных инструментов или методов не требуется). Он идеально подходит для применения в автомобильной, морской и авиакосмической промышленности и часто используется для производства спортивных товаров.
Примеры изделий из стекловолокна
Арт. | Описание | |
---|---|---|
Ткань из стекловолокна 4 унции | Эта ткань из стекловолокна полотняного переплетения плотностью 4 унции является популярным выбором для использования в качестве поверхностной ткани, с достаточной плотностью, с которой легко обращаться.Это обеспечит равномерную прочность как в горизонтальном, так и в вертикальном направлениях. Эта ткань бывает шириной 50 дюймов. | |
Ткань из стекловолокна 7-1 / 2 унции | Ткань весом 7-1 / 2 унции, одна из самых популярных в отрасли стекловолоконных материалов, является фаворитом для гидроизоляции и защиты различных морских объектов, таких как лодки и гидроциклы.![]() | |
Стиль 7781 E-Glass | Style 7781 — это ткань с атласным переплетением, которая часто используется в аэрокосмической и строительной отраслях, предлагая отличную прочность и поверхностные характеристики.Эта ткань бывает шириной 38 и 50 дюймов. |
Усиление Kevlar®
Кевлар® был одним из первых высокопрочных синтетических волокон, получивших признание в индустрии армированного волокном пластика (FRP). Кевлар® из композитов легок, имеет превосходную удельную прочность на разрыв и отличается высокой устойчивостью к ударам и истиранию. Общие области применения включают легкие корпуса лодок, такие как байдарки и каноэ, панели фюзеляжа самолетов и сосуды высокого давления.Кевлар® следует использовать с эпоксидной или винилэфирной смолой.
Кевлар
трудно резать, шлифовать и обрабатывать, и он не подходит для применений, требующих прочности на сжатие.
Технический совет:
Используйте отдельные ножницы для резки кевлара®, потому что стеклоткань изнашивается ножницами под другим углом резки, чем кевлар®. Одни и те же ножницы можно использовать для резки стекла и графита.
Примеры изделий из кевлара
Арт. | Описание | |
---|---|---|
Кевларовая ткань саржевого переплетения | Эта кевларовая ткань идеально подходит для ударопрочных материалов, требующих превосходной удельной прочности на разрыв и минимального веса.Рисунок саржевого переплетения для улучшения драпируемости и косметики. Эта ткань бывает шириной 50 дюймов. | |
Ткань полотняного переплетения кевлар | Популярная кевларовая ткань, полотняное переплетение кевлара, обеспечивает более однородные свойства по сравнению с тканью саржевого переплетения.![]() | |
Кевлар, гибрид из углеродного волокна | Смесь лучших как кевлара, так и углеродного волокна, эта ткань сочетает в себе свойства двух волокон в каждом слое, обеспечивая высокое соотношение прочности и веса, высокую пластичность, ударопрочность, стойкость к истиранию, стабильность размеров и сопротивление усталости. . |
Усиление из углеродного волокна
Графитовые волокна содержат до 95% углерода и обеспечивают самый высокий предел прочности при растяжении в промышленности FRP.Это сила, необходимая, чтобы тянуть за оба конца любой длины, пока он не сломается. Фактически, они также обладают самой высокой прочностью на сжатие и изгиб или изгиб в отрасли. При обработке эти волокна объединяются, чтобы создать армирующее углеродное волокно, такое как ткань, жгут и рукав. Эти арматуры обеспечивают самую высокую прочность и соотношение жесткости к весу в отрасли — больше, чем любые другие обычные арматуры и даже самые традиционные строительные материалы. Углеродное волокно также обеспечивает желанную гладкую черную косметику.
Углеродное волокно обычно дороже других армирующих материалов. И, как только вы достигнете предельной прочности углеродного волокна, выхода не будет: оно внезапно сломается и сломается или расколется.
Технический совет:
Чтобы максимизировать прочностные свойства угля, его следует использовать с эпоксидной смолой, и он может быть отвержден с использованием стандартных методов ламинирования (никаких специальных инструментов или методов не требуется). Он идеально подходит для применения в автомобильной, морской и авиакосмической промышленности и часто используется для производства спортивных товаров.
Примеры изделий из углеродного волокна
Арт. | Описание | |
---|---|---|
3k, полотняного переплетения | Для легких аэродинамических деталей обычно выбирается это углеродное волокно с полотняным переплетением, обеспечивающее одинаковую прочность как в вертикальном, так и в горизонтальном направлениях. Это полотняное переплетение имеет ширину 50 дюймов. | |
3k, 2 x 2 Саржевое переплетение | Наша самая популярная ткань из углеродного волокна с характерным внешним видом, который очень желателен для современных композитных деталей. Саржевое переплетение обеспечивает большую податливость и небольшое преимущество по прочности по сравнению с аналогами с полотняным переплетением. Саржевое переплетение бывает шириной 50 и 60 дюймов. | |
1k, полотняного переплетения | Эта ткань часто используется в самых сложных условиях, когда требуется максимальная прочность и жесткость, а минимальный вес оправдывает добавленную стоимость.Углеродное волокно Plain Weave толщиной 1k имеет ширину 42 дюйма. |
Бетон, армированный углеродным волокном, ускоряется в Германии
Визуализация здания CUBE в Техническом университете Дрездена и карбоновая сетка Hitexbau. Источник | © Юрий Вакалюк, HENN, TU Dresden и Hitexbau.
Технический университет Дрездена в Германии объявил о начале строительства своего демонстрационного дома C³ tech CUBE, известного как Carbonhaus.TU Dresden утверждает, что двухэтажное здание площадью 220 квадратных метров станет первым в мире зданием, полностью построенным из бетона, армированного углеродным волокном.
CUBE демонстрирует бетон, армированный углеродным волокном, через бесшовную бетонную стену длиной 24 метра и «поворот», объединяющий стену и крышу в единую конструкцию с двойным изгибом. Источник | ТУ Дрезден, HENN
Финансируемый Федеральным министерством образования и исследований Германии, проект стоимостью 5 миллионов евро стартовал в 2017 году и завершится весной 2021 года в здании университета, включающем классную комнату, лабораторию и помещения для презентаций.Хотя фундамент был заложен в марте 2020 года, дальнейшее строительство возобновилось только сейчас из-за задержки, вызванной коронавирусом.
Дизайн, усовершенствованный мюнхенской архитектурной фирмой HENN, демонстрирует легкий вес и формуемость бетона, армированного углеродным волокном, благодаря его «скручивающемуся» элементу и, как сообщил Джон Колфилд в статье Building Design + Construction , длиной 24 метра. бесшовных бетонных стен.
«Твист» образован двумя панцирными элементами, которые служат стеной и крышей.Другой основной элемент — это сборный двухуровневый короб. Для обеих секций используется бетон, армированный углеродным волокном. После завершения строительство будет около 40 метров в длину, 7,2 метра в ширину и 6,9 метра в высоту.
Визуализация демонстратора CUBE внутри, смотрящего на сборный коробчатый элемент. Источник | © Юрий Вакалюк, HENN, TU Dresden
Согласно описанию Дрезденского института бетонных конструкций Технического университета, цель этого проекта — показать и продемонстрировать на реальной конструкции, что бетон, армированный углеродом, практичен и практичен.
Новый научно-исследовательский центр углеродного бетона
TU Dresden продолжит дальнейшую работу с углеродным армированным бетоном через совместный исследовательский центр, финансируемый Немецким исследовательским фондом (DFG, Бонн), как было объявлено 6 июня.
Проект C³ — Carbon Concrete Composite в настоящее время является крупнейшим исследовательским проектом в строительной отрасли Германии. Углеродобетон из композитного материала исследуется, разрабатывается и все шире применяется на практике (с 2006 г.) с помощью консорциума, состоящего из более чем 150 партнеров и более 300 индивидуальных проектов.
Самый широко используемый в мире материал после воды — бетон — всегда приводил к высокому расходу сырья. Только на производство цемента приходится 6,5% общих выбросов углекислого газа, что примерно в три раза превышает выбросы CO 2 мировой авиацией.
Посвященный исследованию новых стратегий строительства с использованием бетона
, армированного углеродным волокном, 12 миллионов евро в течение 4 лет будут профинансированы 26 исследователям. Они будут стремиться не только к замене прежнего бетона, армированного сталью, но и разрабатывать новые стратегии проектирования, адаптированные к свойствам бетона, армированного углеродным волокном.
Д-р Манфред Курбах, давний исследователь углеродного волокна и текстильного бетона из TU Dresden, возглавляет этот проект: «Строительство будущего: CRC / TR 280 Стратегии проектирования конструкций из углеродного бетона с минимальным использованием материал — основы нового способа строительства ».
Партнерами
являются RWTH Ахенский университет (Ахен, Германия) и Институт полимерных исследований им. Лейбница (IPF, Дрезден). Отрывок из синопсиса проекта объясняет:
«Новые материалы позволяют создавать новые конструкции и новые методы строительства.Это звучит довольно просто, но зачастую предстоит еще долгий путь. В архитектурном проектировании инновационные процессы занимают особенно много времени из-за высоких требований к безопасности и долговечности, а также сложных процедур стандартизации и утверждения. Это тем более справедливо для сочетаний высокоэффективных строительных материалов, таких как текстильно-армированный бетон и углеродный бетон, что приведет к смене парадигмы, если не к революции в строительстве из бетона, самого важного строительного материала во всем мире с точки зрения объема.
«Использование углеродного бетона может значительно снизить как огромное потребление ресурсов, так и выбросы CO 2 в строительной отрасли, в то же время предоставляя доступ к дополнительным функциям. Однако первые строительные проекты показали, что, несмотря на новые возможности,… обычные материалы просто заменяются. Полный потенциал инновационного композитного материала из углеродного бетона будет реализован в будущем только в том случае, если он будет сочетаться с разумными стратегиями проектирования.
C³-Carbon Concrete Composite был удостоен награды German Sustainability Award 2015. Член консорциума C³ VDZ (Дюссельдорф) участвовал в исследованиях, направленных на устранение рыночных барьеров, создав основу для четких правил (на основе Технического отчета DIN 100) по созданию бетона, армированного углеродным волокном. в строительной практике Германии. Источник | © Ульрих ван Стиприан, C³-Carbon Concrete Composite и VDZ
«Глубокие фундаментальные исследования, а также целостный подход являются предпосылками для поиска подходящих методов проектирования, моделирования и проектирования с использованием новых строительных материалов.Для композитного углеродного бетона это подразумевает принципы облегченной конструкции, адаптированные к материалу. … Разработка новых структур тесно связана с вопросами технологичности, принимая во внимание как сопутствующую оценку устойчивости продукта, так и надлежащую переработку самого композита.
«Стратегии строительства, которые окажутся эффективными, позволят создавать совершенно разные формы. Новые стратегии проектирования и комбинации материалов позволят сократить потребление ресурсов и энергии благодаря ранее неизвестным принципам облегчения конструкции, в то же время обеспечивая высокую пригодность для использования, структурную безопасность и долговечность.Кроме того, эти новые стратегии и композиции отражаются в амбициозной эстетике, которая может развиться в новое «искусство конструирования» ».
Углеродное волокно для армирования больших объемов бетона
Решетка из углеродного волокна для армирования бетона, производства Hitexbau. Источник | Hitexbau
Новостной репортаж «Бетонная арматура из углерода в больших объемах» был опубликован в январе 2020 года издательством Breton, а затем в марте BFT International , признанным отраслевым журналом производителей бетона и сборных железобетонных изделий.Компания Hitexbau (Аугсбург, Германия) разработала высокоавтоматизированную производственную линию для армирования углеродным волокном, позволяющую производить как большие размеры, так и большие объемы. Решетки доступны в виде рулонов или листов и, как сообщается, позволяют использовать бетон с большим диаметром зерна до 16 миллиметров.
В сочетании со специальными покрытиями текстильных арматурных конструкций и с различными рецептурами бетона, Hitexbau утверждает, что эти арматуры позволяют получить бетон с максимальной прочностью на сжатие 3300 ньютонов на квадратный метр.
С 2015 года Hitexbau тесно сотрудничает с TU Dresden и RWTH Aachen в разработке текстильных армирующих материалов из углеродного волокна для строительства. Помимо поставки арматуры, он предлагает разработку продукции и лабораторные испытания.
Примечание редактора: Altus Group (Гринвилл, Южная Каролина, США) — это альянс производителей сборного железобетона, который приносит инновационные технологии на строительный рынок. По состоянию на 2017 год его члены выполнили более 1400 проектов с использованием технологии CarbonCast, армированной углепластиком, на общую сумму 40 миллионов футов 2 (3.7 млн м 2 ). Пожалуйста, прочтите о технологии CarbonCast, разработанной совместно с Chomarat North America (Уильямстон, Южная Америка) с использованием продукта C-GRID, в статье 2017 года: «Более высокие характеристики сборного железобетона с использованием углепластика».
Углеродные волокна: производство, свойства и возможности использования
Пуджа Бхатт и Алка Го
Старший научный сотрудник, профессор и заведующий кафедрой одежды и текстиля, Г.B.P.U.A and T, Пантнагар,
Автор, ответственный за переписку Электронная почта: [email protected]
DOI: http://dx.doi.org/10.13005/msri/140109
История публикации статьи
Статья получена: 30 мая 2017 г.
Статья принята: 5 июня 2017 г.
Статья опубликована: 9 июня 2017 г.
Проверка на плагиат: Да
АННОТАЦИЯ:
Углеродное волокно состоит из атомов углерода, связанных вместе, образуя длинную цепочку.Волокна чрезвычайно жесткие, прочные и легкие и используются во многих процессах для создания превосходных строительных материалов. Углеродный волокнистый материал входит в состав множества «сырых» строительных блоков, включая пряжу, однонаправленную пряжу, переплетения, тесьму и некоторые другие, которые, в свою очередь, используются для создания композитных деталей. Детали из углеродного волокна по своим свойствам близки к стальным, а по весу — к пластиковым. Таким образом, отношение прочности к весу (а также отношение жесткости к весу) детали из углеродного волокна намного выше, чем у стали или пластика.Углеродное волокно чрезвычайно прочное. В инженерии обычно измеряют преимущество материала с точки зрения отношения прочности к весу и отношения жесткости к весу, особенно при проектировании конструкций, где добавленный вес может привести к увеличению стоимости жизненного цикла или неудовлетворительным характеристикам.
КЛЮЧЕВЫЕ СЛОВА:
Углеродное волокно; Ткань; Текстиль; Пряжа
Чтобы процитировать эту статью, скопируйте следующее: Bhatt P, Goe A. Углеродные волокна: производство, свойства и потенциальное использование.Математические науки и ресурсы Индии; 14 (1) |
Введение
Углеродные волокна или углеродные волокна — это волокна диаметром около 5–10 микрометров, состоящие в основном из атомов углерода. Углеродные волокна обладают рядом преимуществ, включая высокую жесткость, высокую прочность на разрыв, малый вес, высокую химическую стойкость, устойчивость к высоким температурам и низкое тепловое расширение. Эти свойства сделали углеродное волокно очень популярным в аэрокосмической отрасли, гражданском строительстве, вооруженных силах и автоспорте, а также в других соревновательных видах спорта.Однако они относительно дороги по сравнению с аналогичными волокнами, такими как стекловолокно или пластмассовые волокна.
Классификация и типы
Углеродные волокна по модулю упругости, прочности и конечной температуре термообработки можно разделить на следующие категории:
По свойствам углеродного волокна углеродные волокна можно сгруппировать в:
- Сверхвысокий модуль, тип UHM (модуль> 450 ГПа)
- Высокомодульный, тип HM (модуль упругости 350-450 ГПа)
- Промежуточный модуль, тип IM (модуль между 200-350 ГПа)
- Низкомодульный и высокопрочный, тип HT (модуль <100 ГПа, предел прочности> 3.0 ГПа)
- Сверхвысокопрочный, тип SHT (предел прочности на разрыв> 4,5 ГПа)
Углеродные волокна на основе материалов-предшественников подразделяются на:
- Углеродные волокна на основе ПАН
- Углеродные волокна на основе пека
- Углеродные волокна на основе мезофазного пека
- Углеродные волокна на основе изотропного пека
- Углеродные волокна на основе вискозы
- Углеродные волокна, выращенные в газовой фазе
Углеродные волокна по температуре окончательной термообработки подразделяются на:
- Углеродные волокна с высокой термической обработкой (HTT), тип I, где конечная температура термообработки должна быть выше 2000 ° C и может быть связана с волокном высокомодульного типа.
- Углеродные волокна с промежуточной термообработкой (IHT), тип II, где конечная температура термообработки должна быть около или выше 1500 ° C и может быть связана с волокном высокопрочного типа.
- Углеродное волокно с низкой термической обработкой, тип III, температура конечной термообработки которого не превышает 1000 ° C. Это низкомодульные и малопрочные материалы.
Производственный процесс
Углеродные волокна из полиакрилонитрила (PAN):
Сырье
Сырье, используемое для производства углеродного волокна, называется прекурсором.Около 90% производимых углеродных волокон состоит из полиакрилонитрила. Остальные 10% сделаны из искусственного шелка или нефтяного пека. Все эти материалы представляют собой органические полимеры, характеризующиеся длинными цепочками молекул, связанных вместе атомами углерода. Точный состав каждого прекурсора варьируется от одной компании к другой и обычно считается коммерческой тайной. В процессе производства используются различные газы и жидкости. Некоторые из этих материалов предназначены для взаимодействия с волокном для достижения определенного эффекта.Другие материалы предназначены для того, чтобы не вступать в реакцию или предотвращать определенные реакции с волокном. Как и в случае с прекурсорами, точный состав многих из этих технологических материалов считается коммерческой тайной.
Производственный процесс PAN
Рисунок 1
Прядильная
- Порошок акрилонитрильного пластика смешивают с другим пластиком, таким как метилакрилат или метилметакрилат, и подвергают взаимодействию с катализатором в обычном процессе суспензионной или растворной полимеризации с образованием полиакрилонитрильного пластика.
- Затем пластик превращается в волокна одним из нескольких различных методов. В некоторых методах пластик смешивается с определенными химическими веществами и закачивается через крошечные форсунки в химическую ванну или камеру закалки, где пластик коагулирует и затвердевает в волокна. Это похоже на процесс, используемый для формирования полиакриловых текстильных волокон. В других методах пластиковая смесь нагревается и перекачивается через крошечные форсунки в камеру, где растворители испаряются, оставляя твердое волокно. Этап прядения важен, потому что во время этого процесса формируется внутренняя атомная структура волокна.
- Затем волокна промывают и растягивают до желаемого диаметра. Растяжение помогает выровнять молекулы внутри волокна и обеспечивает основу для образования прочно связанных кристаллов углерода после карбонизации.
Стабилизирующий
Перед карбонизацией волокон их необходимо химически изменить, чтобы преобразовать их линейную атомную связь в более термически стабильную лестничную связь. Это достигается путем нагревания волокон на воздухе примерно до 390-590 ° F (200-300 ° C) в течение 30-120 минут.Это заставляет волокна улавливать молекулы кислорода из воздуха и изменять структуру их атомных связей. Стабилизирующие химические реакции сложны и включают несколько этапов, некоторые из которых происходят одновременно. Они также генерируют собственное тепло, которое необходимо контролировать, чтобы избежать перегрева волокон. В коммерческих целях для процесса стабилизации используется различное оборудование и методы. В некоторых процессах волокна протягиваются через ряд камер с подогревом. В других случаях волокна проходят через горячие валки и через слои сыпучих материалов, удерживаемых во взвешенном состоянии потоком горячего воздуха.В некоторых процессах используется нагретый воздух, смешанный с определенными газами, которые химически ускоряют стабилизацию.
Карбонизация
После стабилизации волокон их нагревают до температуры примерно 1,830-5,500 ° F (1,000-3,000 ° C) в течение нескольких минут в печи, заполненной газовой смесью, не содержащей кислорода. Недостаток кислорода предотвращает сгорание волокон при очень высоких температурах. Давление газа внутри печи поддерживается выше, чем давление наружного воздуха, а точки входа и выхода волокон из печи герметизированы, чтобы не допустить попадания кислорода.Когда волокна нагреваются, они начинают терять свои неуглеродные атомы, а также несколько атомов углерода в виде различных газов, включая водяной пар, аммиак, монооксид углерода, диоксид углерода, водород, азот и другие. Когда неуглеродные атомы вытесняются, оставшиеся атомы углерода образуют прочно связанные углеродные кристаллы, которые ориентированы более или менее параллельно длинной оси волокна. В некоторых процессах используются две печи, работающие при двух разных температурах, чтобы лучше контролировать скорость разогрева во время карбонизации.
Рисунок 2
Обработка поверхности
После карбонизации волокна имеют поверхность, которая плохо сцепляется с эпоксидными смолами и другими материалами, используемыми в композитных материалах. Чтобы волокна лучше склеивали, их поверхность слегка окисляется. Добавление атомов кислорода к поверхности обеспечивает лучшие свойства химического связывания, а также травит и делает поверхность шероховатой для улучшения механических свойств связывания.Окисление может быть достигнуто путем погружения волокон в различные газы, такие как воздух, диоксид углерода или озон; или в различных жидкостях, таких как гипохлорит натрия или азотная кислота. На волокна также можно нанести электролитическое покрытие, сделав волокна положительным выводом в ванне, заполненной различными электропроводящими материалами. Процесс обработки поверхности необходимо тщательно контролировать, чтобы избежать образования крошечных дефектов поверхности, таких как ямки, которые могут вызвать повреждение волокна.
Калибр
- После обработки поверхности волокна покрываются покрытием для защиты от повреждений при намотке или плетении.Этот процесс называется калибровкой. Материалы покрытия выбираются таким образом, чтобы они были совместимы с клеем, используемым для формирования композитных материалов. Типичные материалы покрытия включают эпоксидную смолу, полиэстер, нейлон, уретан и другие.
- 8 Волокна с покрытием наматываются на цилиндры, называемые бобинами. Бобины загружаются в прядильную машину, и волокна скручиваются в пряжу различных размеров.
Недвижимость
Углеродное волокно имеет высокое отношение прочности к массе (также известное как удельная прочность)
Прочность материала — это сила, приходящаяся на единицу площади при разрушении, деленная на его плотность.Любой прочный И легкий материал имеет подходящее соотношение прочности и веса. Такие материалы, как алюминий, титан, магний, углеродное волокно и стекловолокно, высокопрочные стальные сплавы, имеют хорошее соотношение прочности к весу.
Углеродное волокно очень жесткое
Жесткость или жесткость материала измеряется его модулем Юнга и измеряет, насколько материал прогибается под действием напряжения. Пластик, армированный углеродным волокном, более чем в 4 раза жестче, чем пластик, армированный стекловолокном, почти в 20 раз больше, чем сосна, 2.В 5 раз больше алюминия.
Углеродное волокно устойчиво к коррозии и химически стабильно
Хотя углеродное волокно само по себе не портится, эпоксидная смола чувствительна к солнечному свету и требует защиты. Другие матрицы (независимо от того, в какое углеродное волокно встроено) также могут быть реактивными.
Углеродное волокно электропроводное
Эта функция может быть полезной и мешать. При строительстве лодок это необходимо учитывать, так как в игру вступает проводимость алюминия.Электропроводность углеродного волокна может способствовать гальванической коррозии арматуры. Тщательная установка может уменьшить эту проблему.
Усталостное сопротивление хорошее
Устойчивость к усталости композитов из углеродного волокна — хорошая. Однако, когда углеродное волокно выходит из строя, оно обычно катастрофически выходит из строя, и это не говорит о его неизбежном разрыве. Повреждение в результате усталости при растяжении рассматривается как снижение жесткости при увеличении количества циклов напряжения (если температура не высокая). Испытания показали, что разрушение вряд ли будет проблемой, когда циклические напряжения совпадают с ориентацией волокна.Углеродное волокно превосходит стекло E по усталостной и статической прочности, а также по жесткости.
Углеродное волокно имеет хорошую прочность на разрыв
Прочность на растяжение или предел прочности — это максимальное напряжение, которое может выдержать материал при растяжении или растяжении до образования шейки или разрушения. Сужение — это когда поперечное сечение образца начинает значительно сокращаться. Если вы возьмете полоску полиэтиленового пакета, она растянется и в какой-то момент начнет сужаться. Это шею.Он измеряется в силе на единицу площади. Хрупкие материалы, такие как углеродное волокно, не всегда выходят из строя при одном и том же уровне напряжения из-за внутренних дефектов. Они терпят неудачу при малых деформациях.
Испытание включает взятие образца с фиксированной площадью поперечного сечения, а затем его вытягивание, постепенно увеличивая силу, пока образец не изменит форму или не сломается. Волокна, такие как углеродные волокна, имеющие диаметр всего 2/10 000-х дюйма, превращаются в композиты соответствующей формы для испытаний.
Огнестойкость / невоспламеняющийся
В зависимости от производственного процесса и материала-прекурсора углеродное волокно может быть довольно мягким и может использоваться в качестве защитной одежды для пожарных или, что более часто, интегрировано в нее.Примером может служить волокно с никелевым покрытием. Поскольку углеродное волокно также химически очень инертно, его можно использовать там, где есть огонь в сочетании с коррозионными агентами. Carbon Fiber Fire Blanket извините за опечатки.
Теплопроводность углеродного волокна
Теплопроводность — это количество тепла, передаваемого через единицу толщины в направлении, нормальном к поверхности единицы площади, из-за единичного температурного градиента в установившихся условиях. Другими словами, это показатель того, насколько легко тепло проходит через материал.
Поскольку существует множество вариаций углеродного волокна, невозможно точно определить теплопроводность. Специальные типы углеродного волокна были специально разработаны для обеспечения высокой или низкой теплопроводности. Также предпринимаются попытки улучшить эту функцию.
Низкий коэффициент теплового расширения
Это мера того, насколько материал расширяется и сжимается при повышении или понижении температуры. Единицы измерения указаны в дюймах / дюймах градусах F. Как и в других таблицах, единицы измерения не так важны, как сравнение.При достаточно высокой мачте разница в коэффициентах теплового расширения различных материалов может немного изменить натяжение буровой установки. Низкий коэффициент теплового расширения делает углеродное волокно подходящим для применений, где малые движения могут быть критичными. Одно из таких приложений — телескоп и другое оптическое оборудование.
Неядовит, биологически инертен, проницаем для рентгеновских лучей
Эти качества делают углеродное волокно полезным в медицине. В разработке находятся протезы, имплантаты и восстановление сухожилий, рентгеновские аксессуары, хирургические инструменты.Углеродные волокна не ядовиты, но могут вызывать сильное раздражение, поэтому необходимо ограничить длительное незащищенное воздействие. Однако эпоксидная или полиэфирная матрица может быть токсичной, поэтому необходимо соблюдать осторожность.
Углеродное волокно относительно дорогое
Хотя он предлагает исключительные преимущества прочности, жесткости и снижения веса, его стоимость является сдерживающим фактором. Если преимущество в весе не является исключительно важным, например, в аэронавтике или гонках, оно часто не стоит дополнительных затрат.Дополнительным преимуществом является низкая потребность в обслуживании углеродного волокна.
Трудно количественно охарактеризовать круто и модно. Углеродное волокно имеет ауру и репутацию, которые заставляют потребителей платить больше за то, чтобы иметь его. Возможно, вам понадобится меньше его по сравнению со стекловолокном, и это может быть экономией.
Углеродные волокна хрупкие
Слои волокон образованы прочными ковалентными связями. Листовые агрегаты легко допускают распространение трещин.Когда волокна изгибаются, они выходят из строя при очень низкой деформации.
Приложения
Характеристики и применение углеродных волокон
1. Физическая прочность, удельная вязкость, легкий вес | Авиакосмическая промышленность, автомобильный и морской транспорт, спортивные товары |
2. Высокая стабильность размеров, низкий коэффициент теплового расширения и низкий уровень абразивного износа | Ракеты, авиационные тормоза, аэрокосмическая антенна и опорная конструкция, большие телескопы, оптические стенды, волноводы для стабильных высокочастотных (ГГц) прецизионных измерительных рам |
3.Хорошее гашение вибрации, прочность и ударная вязкость | Аудиотехника, громкоговорители для Hi-Fi аппаратуры, звукосниматели, манипуляторы |
4. Электропроводность | Автомобильные капоты, новая оснастка, кожухи и основания для электронного оборудования, защита от электромагнитных и радиочастотных помех, щетки |
5. Биологическая инертность и рентгеновская проницаемость | Медицинское применение в протезах, хирургическом и рентгеновском оборудовании, имплантатах, восстановлении сухожилий / связок |
6.Усталостная прочность, самосмазывание, высокое демпфирование | Текстильное оборудование общего назначения |
7. Химическая инертность, высокая коррозионная стойкость | Химическая промышленность; ядерное поле; клапаны, уплотнения и компоненты насосов на технологических установках |
8. Электромагнитные свойства | Большие стопорные кольца генератора, радиологическое оборудование |
Заключение
Последняя разработка в технологии углеродного волокна — это крошечные углеродные трубки, называемые нанотрубками.Эти полые трубки, некоторые из которых имеют диаметр 0,00004 дюйма (0,001 мм), обладают уникальными механическими и электрическими свойствами, которые могут быть полезны при создании новых высокопрочных волокон, субмикроскопических пробирок или, возможно, новых полупроводниковых материалов для интегральных схем.
Список литературы
- Франк Э., Херманутц Ф. и Бухмайзер М. Р. Углеродные волокна: прекурсоры, производство и свойства. Макромол. Mater. Eng . 2012; 297: 493–501.
CrossRef - Шаваллер Д., Клаус Б. и Бухмайзер М. Р. Керамические филаментные волокна — Обзор. Макромол . Mater. Eng . 2012: 297: 502–522.
CrossRef - Хо К., Цянь К. К. и Бисмарк Х. А. Углеродное волокно: свойства поверхности. Энциклопедия композитов Wiley . 2011; 1–11.
- Хуанг X. Изготовление и свойства углеродных волокон. Материалы. 2009; 2 : 2369-2403.
CrossRef - Баджадж П.